Failure Analysis su cella di carico
RUBRICA | Come si è rotto? #06TEC EUROLAB
#06
Failure Analysis su Cella di carico
NUOVA RUBRICA | Come si è rotto?
L’oggetto
Una cella di carico è un dispositivo elettronico utilizzato per misurare la forza o il carico applicato su di essa. È composta da una struttura sensibile allo sforzo, generalmente realizzata in lega metallica o materiale ceramico, che reagisce deformandosi quando viene applicato un carico. Questa deformazione viene convertita in un segnale elettrico proporzionale alla forza applicata.
Le celle di carico vengono utilizzate in una vasta gamma di applicazioni, come ad esempio in bilance industriali e commerciali per misurare il peso degli oggetti, in macchinari per il controllo della tensione o della pressione, in veicoli per misurare il carico sugli assi, o in strutture come ponti e gru per monitorare il carico e prevenire sovraccarichi.
Le possibili modalità di failure di una cella di carico possono includere:
- Sovraccarico: l’applicazione di un carico superiore alla capacità massima della cella di carico può causare danni irreversibili alla struttura, compromettendo la sua precisione o addirittura causandone la rottura.
- Sottocarico: se il carico applicato è inferiore alla sensibilità minima della cella di carico, potrebbe non essere in grado di rilevare correttamente il peso o fornire una misurazione accurata.
- Deformazione permanente: se una cella di carico viene sottoposta a carichi oltre il suo limite elastico, potrebbe subire una deformazione permanente che influenzerà la sua precisione e affidabilità.
- Usura meccanica: l’uso prolungato e ripetuto di una cella di carico può causare usura meccanica sui componenti interni, portando a un deterioramento delle prestazioni nel tempo.
- Difetti di fabbricazione: errori di progettazione o problemi nella produzione della cella di carico possono portare a difetti strutturali o a malfunzionamenti che influiscono sulla sua accuratezza e durata nel tempo.
Per mantenere la precisione e la sicurezza delle celle di carico, è importante seguire le specifiche tecniche del produttore, utilizzarle all’interno dei limiti di carico consigliati e sottoporle a una corretta manutenzione.
Scopo dell’indagine
Il Committente ha richiesto al laboratorio una failure analysis sulla cella di carico. L’obiettivo è valutare le possibili cause del cedimento del componente durante il suo utilizzo. La cella di carico si trovava sotto una barra pesatrice, che a sua volta era posizionata sotto dei ponti di pesatura per camion. Durante l’uso, la cella di carico veniva schiacciata dal carico presente sui ponti di pesatura e sulla barra pesatrice, in una condizione di carico simile a una mensola incernierata con una forza concentrata.
Il Committente riporta che il componente si è rotto circa un anno e mezzo dopo essere stato messo in servizio e segnala che anche altri componenti hanno subito cedimenti simili. La rottura del componente è avvenuta a partire dal raggio R2.5 e si è propagata attraverso tutto lo spessore del pezzo, coinvolgendo parzialmente il foro filettato.
Secondo le informazioni fornite dal Committente, la cella di carico è stata fabbricata in acciaio legato da bonifica del tipo 40CrNiMoA, conforme alla norma GB/T 3077-2015. Il materiale è stato fornito nello stato bonificato e lavorato meccanicamente.
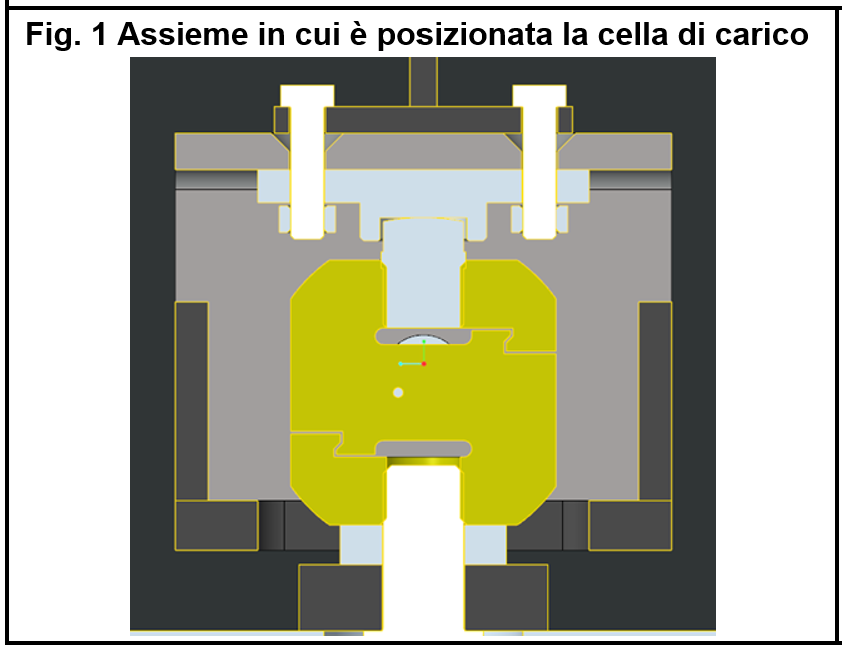
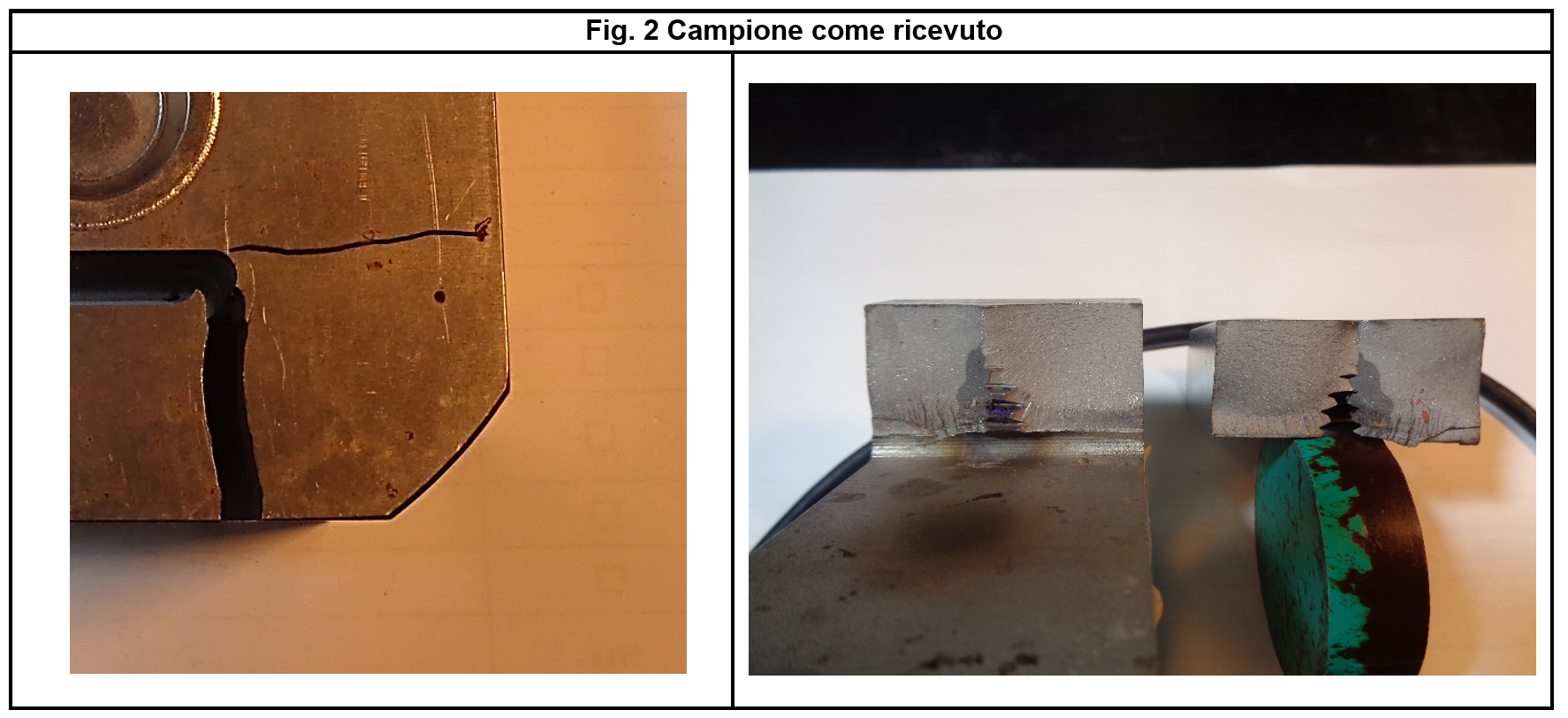
Le analisi
La frattura della cella di carico si è verificata nella zona del raggio R2.5 superiore, interessando parzialmente la filettatura. Le superfici di frattura presentano un aspetto opaco e grigio chiaro, con solchi paralleli e presenza di corrosione agli spigoli esterni. Si ipotizza una rottura per sovraccarico fragile, innescata dagli spigoli esterni e influenzata da un possibile processo corrosivo. La frattura si è propagata alla sezione resistente del componente.
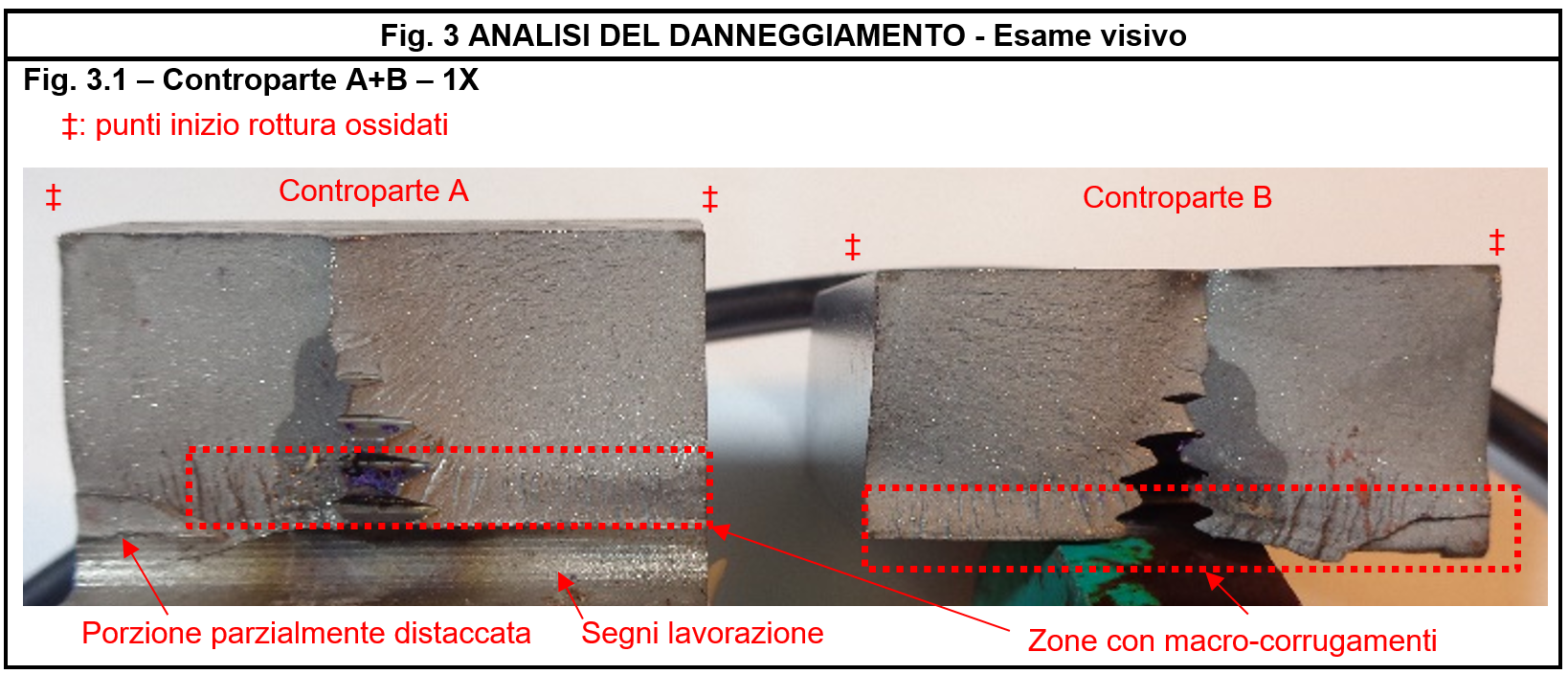
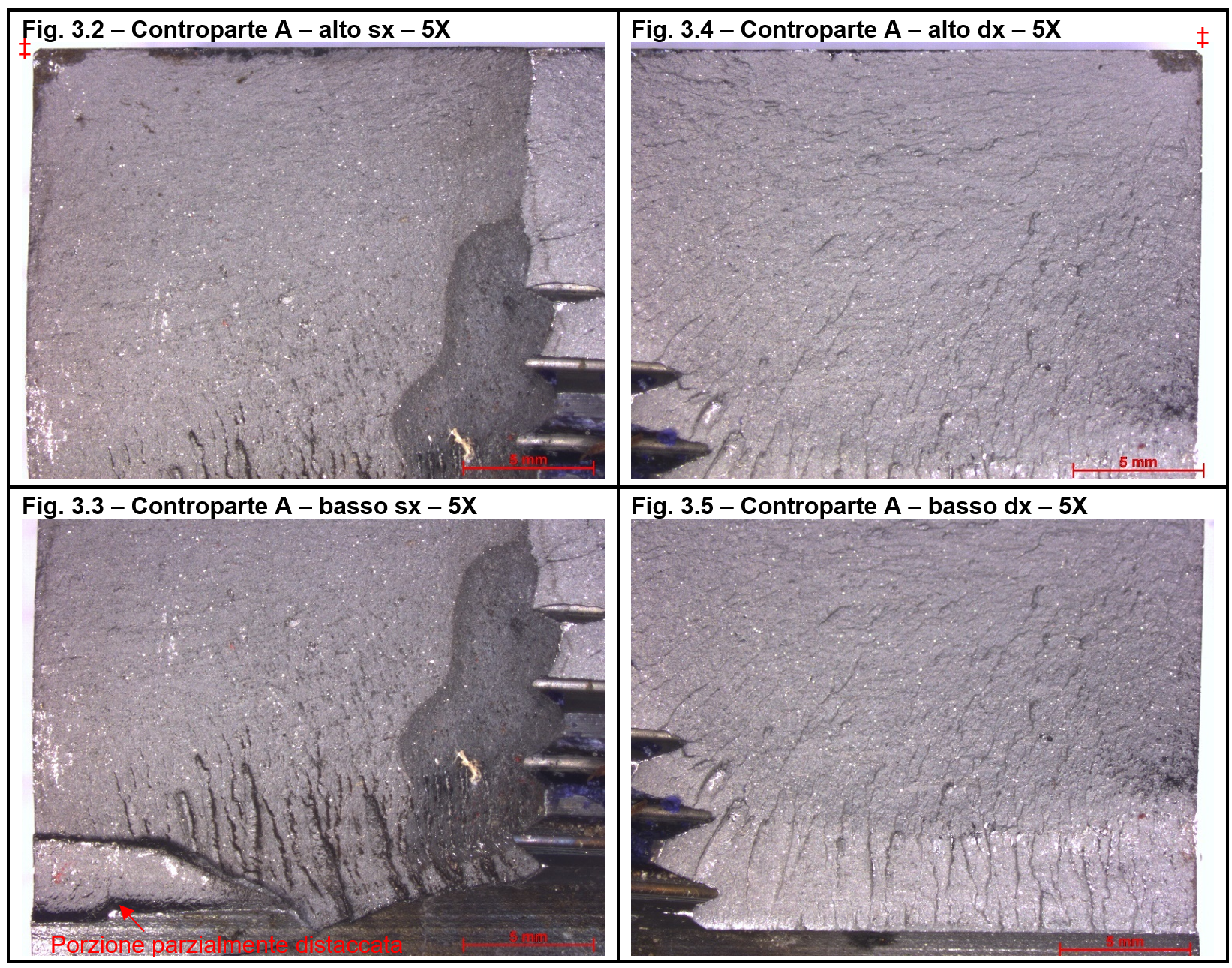
L’analisi morfologica tramite microscopio elettronico a scansione (SEM) e l’analisi elementale con sonda EDS sono state condotte sulla controparte A della cella di carico. Le caratteristiche frattografiche e morfologiche erano simili alla controparte speculare. Sono state osservate morfologie di frattura mista, sia intergranulare che transgranulare, sia nelle zone esterne della frattura vicino agli spigoli che nella parte inferiore della sezione.
L’analisi con sonda EDS ha rivelato una composizione chimica con prevalenza di ferro, ossigeno, cromo e carbonio, e tracce di silicio e cloro. La presenza di ossidazione e l’aumento del tenore di ossigeno nella zona ossidata confermano la presenza di fenomeni corrosivi. La composizione chimica è associata a un acciaio inossidabile ad alto tenore di cromo, a differenza di quanto previsto inizialmente (acciaio legato da bonifica).
L’osservazione frattografica suggerisce che il componente si sia rotto per sovraccarico in regime di rottura fragile. Non sono stati osservati inclusioni o altri difetti metallurgici, ad eccezione delle zone interessate dalla corrosione.
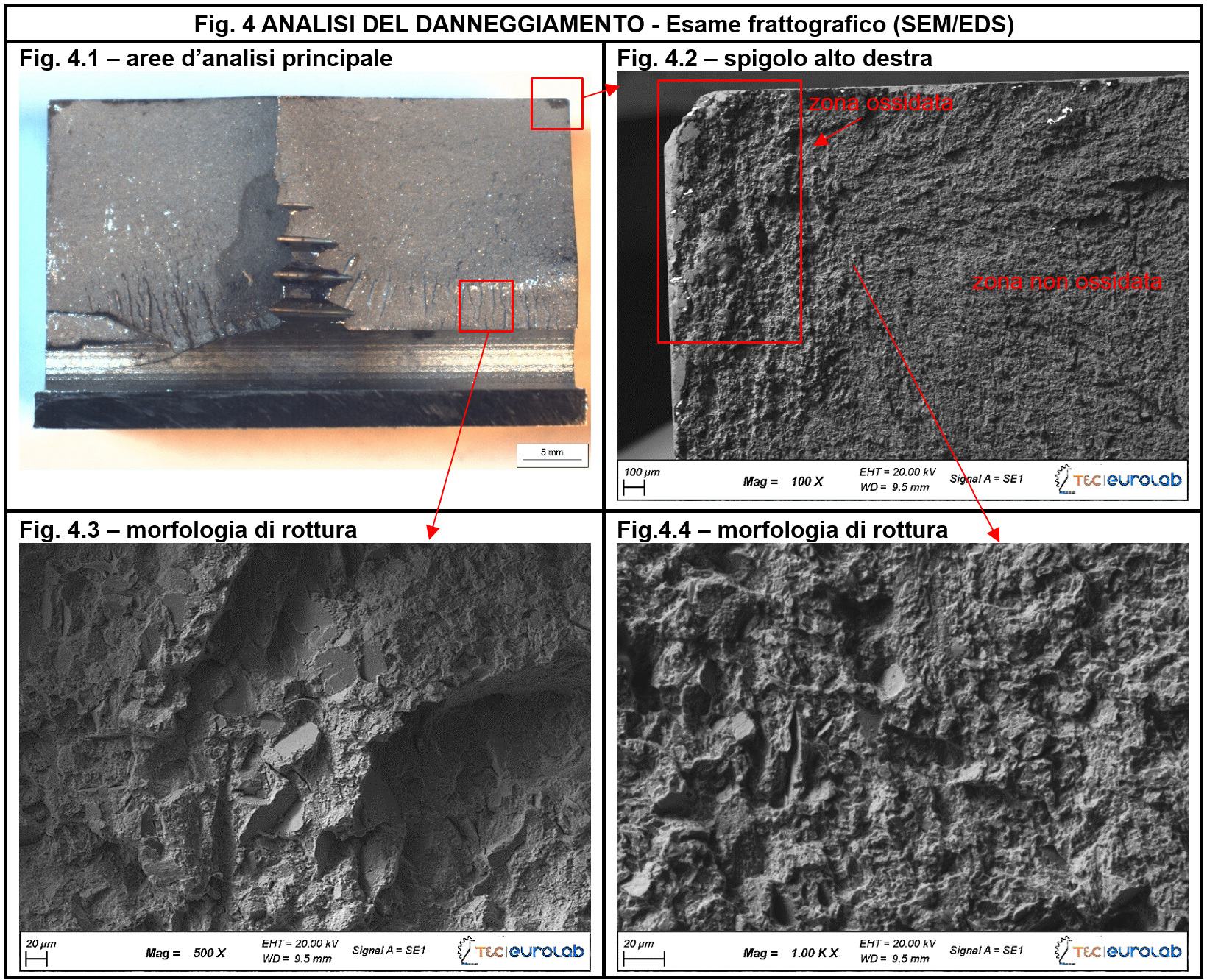
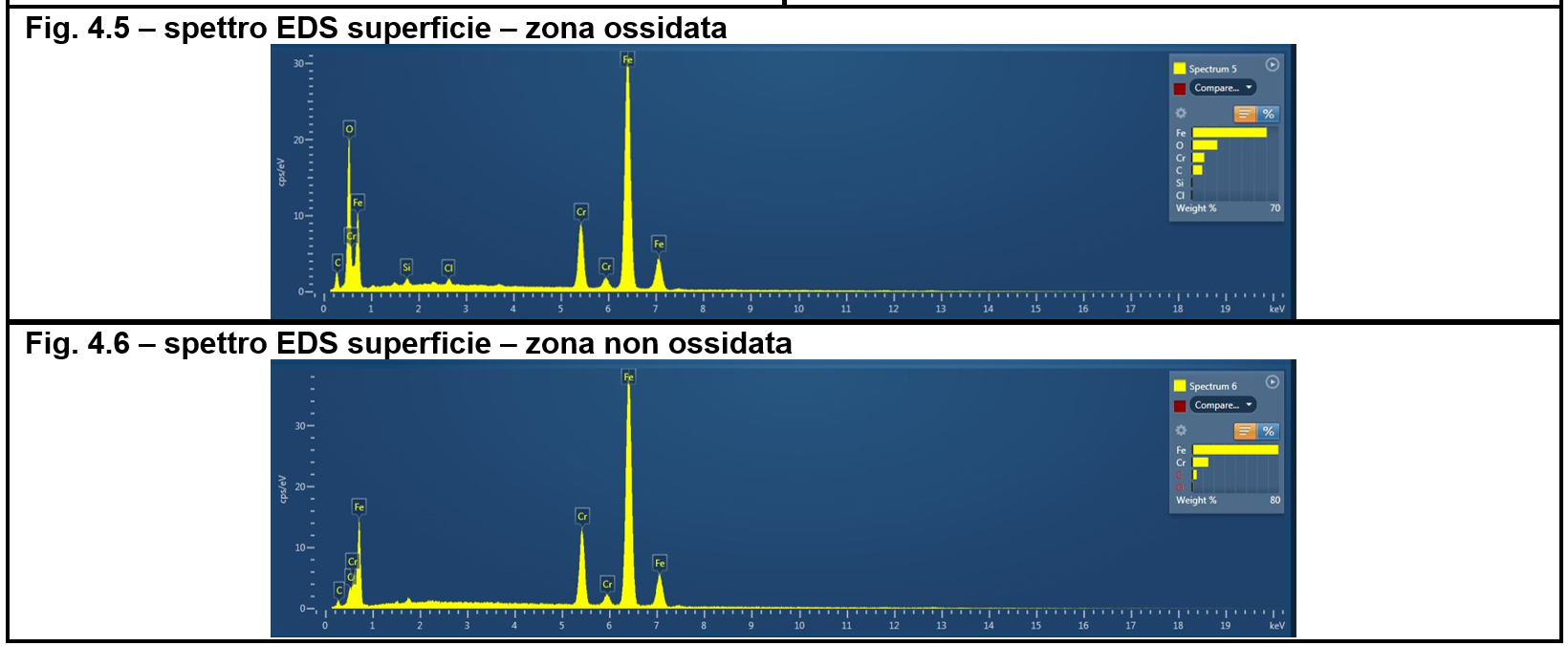
L’analisi micrografica della superficie di frattura è stata condotta su due zone distinte a sinistra e a destra del foro filettato, intercettando le zone interessate dalla corrosione sugli spigoli esterni. Entrambi i profili della superficie di frattura presentavano un aspetto frastagliato lungo il traverso corto del componente, con un profilo meno frastagliato sulla parte interna del lato sinistro. Non sono state osservate zone di schiacciamento o ricalcatura lungo la superficie di frattura.
La frattura presentava un andamento misto, sia intergranulare che transgranulare, coerente con le osservazioni precedenti. Sono state individuate diverse cricche intergranulari sul lato esterno non coinvolto dalla frattura, probabilmente associate a forme di corrosione localizzata.
Le caratteristiche microstrutturali osservate sono simili a quelle precedentemente analizzate. In generale, le evidenze frattografiche confermano quanto osservato nelle analisi precedenti, e non sono state rilevate anomalie o discontinuità metallurgiche nella zona di frattura, ad eccezione delle zone interessate dalla corrosione localizzata.
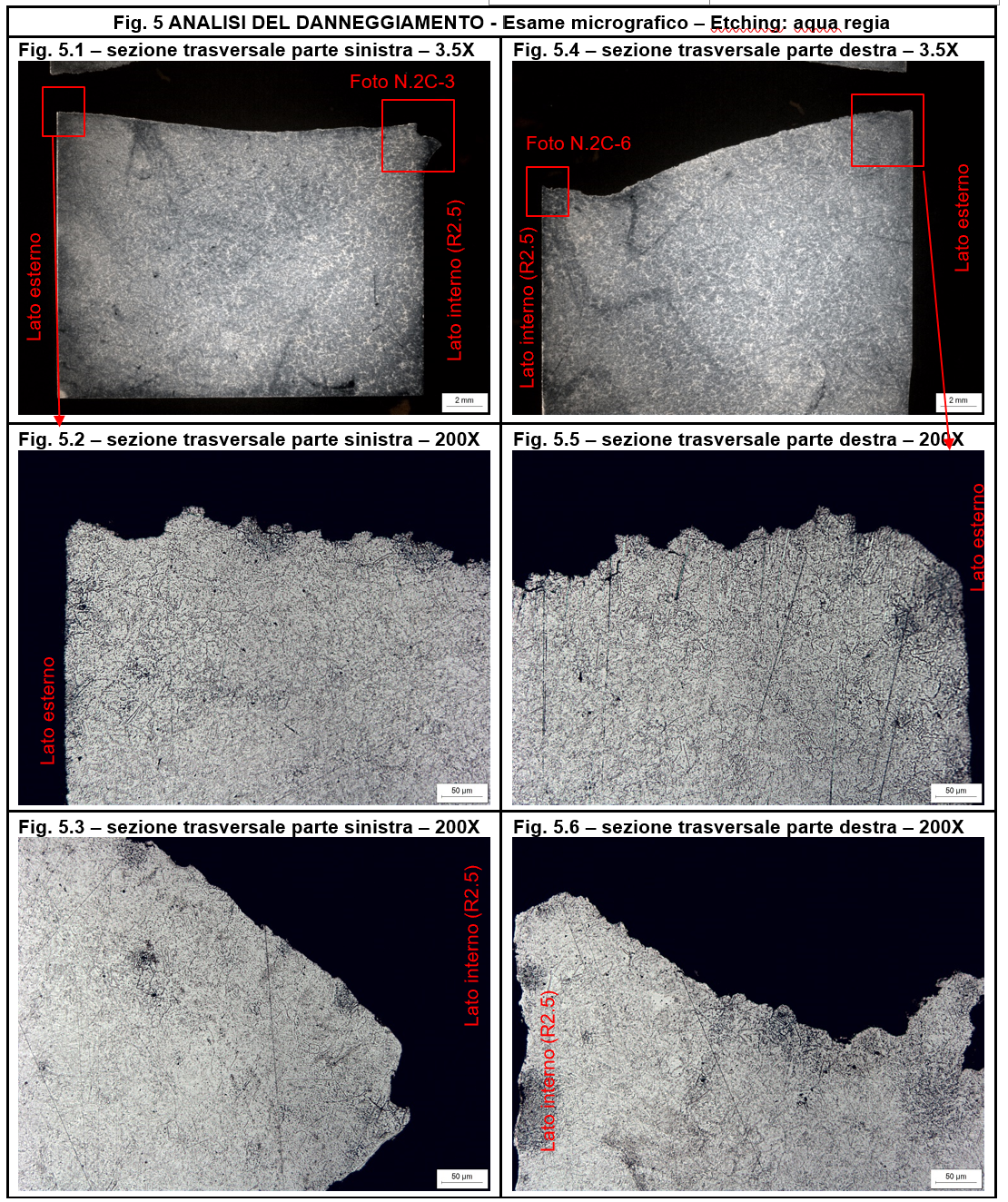
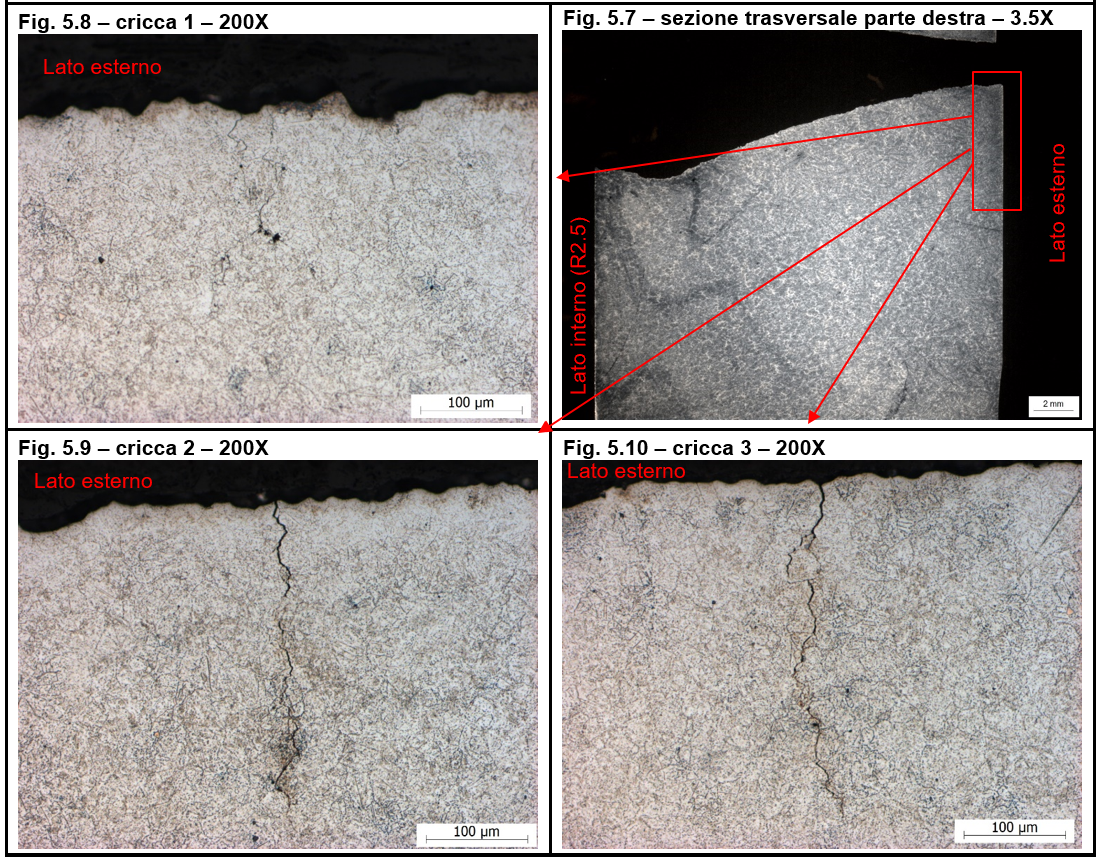
L’analisi del materiale ha rivelato che il componente è costituito da un acciaio inossidabile martensitico del tipo AISI 420 o X30Cr13. Questa classificazione è in contrasto con le informazioni fornite dal Committente riguardo a un acciaio legato da bonifica 40NiCrMoA. L’esame micrografico ha confermato la presenza di martensite distesa e carburi fini dispersi nella microstruttura del materiale, indicando un trattamento termico di tempra e distensione. Non sono state rilevate discontinuità o anomalie microstrutturali.
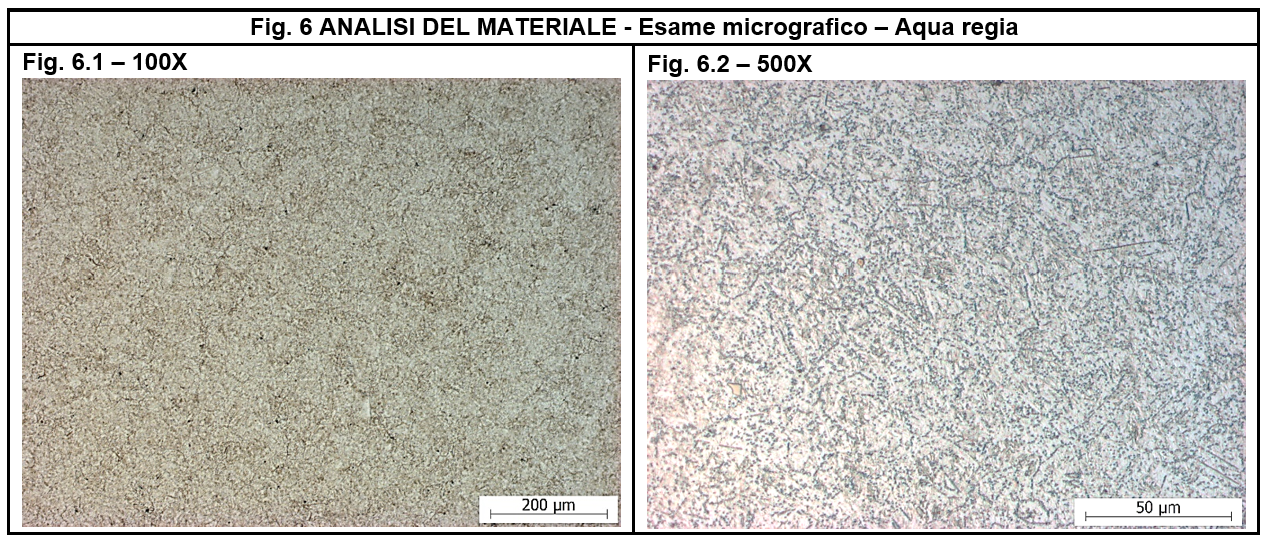
Le prove di trazione e resilienza effettuate sulla cella di carico hanno mostrato risultati che differiscono dalle specifiche UNI EN 10088-3:2014 per lo stato di fornitura +QT850. La norma ASTM A276-13a non fornisce valori minimi per le proprietà meccaniche tensili o di resilienza dell’acciaio AISI 420.
La prova di durezza Rockwell ha rilevato una durezza a cuore del materiale della cella di carico compresa tra 48,5 e 49,0 HRC, che si avvicina alla durezza minima richiesta dalla norma A276-13a per l’acciaio AISI 420 temprato e disteso. La norma UNI EN 10088-3:2014 non specifica i valori minimi di durezza per l’acciaio X30Cr13.
Risultati e Conclusioni
Sulla base delle evidenze raccolte e delle informazioni sull’utilizzo del componente, si ipotizza che la rottura sia dovuta a un sovraccarico meccanico in condizioni di carico flessionale. Non sono state rilevate discontinuità o difetti metallurgici, ad eccezione degli spigoli esterni con segni di corrosione, indicando fenomeni corrosivi locali durante l’uso.
La rottura si presume sia iniziata dagli spigoli esterni del componente, dove è presente il maggior fattore di intensificazione degli sforzi a causa della geometria e della direzione del carico, insieme a segni di corrosione localizzata che potrebbero aver generato e propagato difetti. La rottura si è propagata fino alla zona del raggio R2.5, avvenendo come rottura di schianto.
La caratterizzazione del materiale ha rivelato che il componente è realizzato in acciaio inossidabile martensitico AISI 420 o X30Cr13, a differenza delle informazioni fornite dal Committente riguardo all’acciaio legato da bonifica 40NiCrMoA. Il materiale è stato fornito in condizioni di tempra e distensione, con elevata resistenza e durezza, ma anche intrinseca fragilità come indicato dalla prova di resilienza e di trazione. Questa fragilità, insieme alla bassa resistenza a fenomeni corrosivi localizzati, ha contribuito al danneggiamento e alla rottura del componente, come confermato dalla superficie di frattura.
Vuoi scoprire perchè il tuo componente si è rotto?
Compila il form e sarai ricontattato dal nostro staff tecnico
Leggi gli altri case study sulla Failure Analysis
Failure Analysis su tubo di gomma
Nuovo caso di analisi failure approfondita su un tubo di gomma
Failure Analysis su valigia da viaggio | Rubrica come si è rotto? #09
Come si è rotta una valigia da viaggio? Nuovo case study di failure analysis
Failure Analysis su Perno filettato | Rubrica Come si è rotto? #08
Nuovo case study di Failure Analysis. Scopriamo come si è rotto un perno filettato
Il tuo componente si è rotto in esercizio e vuoi capire qual è la causa della rottura?