TEC EUROLAB
Testing su fasteners
Quali sono i vantaggi per i clienti e quali sono le principali evoluzioni del settore della viteria nel prossimo futuro.
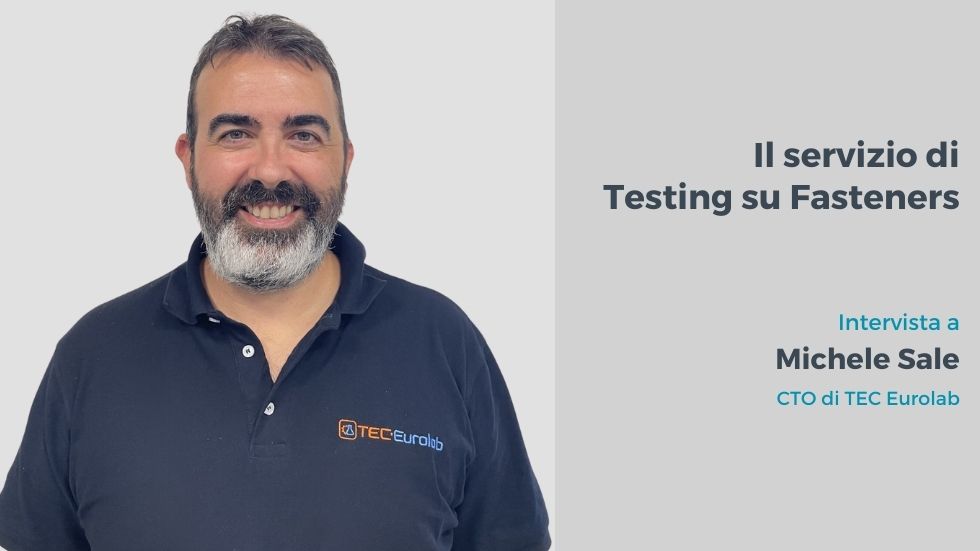
Il servizio di testing sui Fasteners di TEC Eurolab
Il nostro CTO Michele Sale propone una panoramica sul servizio di Testing su Fasteners: perchè è importante, con quali aziende collaboriamo, quali sono i vantaggi per i clienti e quali sono le principali evoluzioni del settore della viteria nel prossimo futuro.
A quali tipologie di aziende si rivolge questo tipo di servizio? Viene richiesto da aziende di settori specifici o trova interesse in vari ambiti industriali?
TEC Eurolab opera come laboratorio nel settore della viteria ormai da vent’anni, conducendo attività di controllo lotti e testing di qualifica/verifica lotto in ingresso presso i clienti che acquistano anche a stock. il primo cliente aeronautico in assoluto è stato infatti il principale distributore di viteria aeronautica noto a livello nazionale ed ormai internazionale, che vanta i principali OEM aeronautici che operano sia nell’ambito civile che militare. Partendo da questa esperienza, si è ampliato il servizio su altri distributori e produttori di viteria, ampliando sia il numero dei clienti in ambito aeronautico serviti, sia i settori, con automotive e biomedicale in primis.
Tra le attività core di testing per TEC Eurolab figurano le prove su elementi di collegamento meccanico, parlando di fasteners. Potresti dare una veloce panoramica del servizio e delle tipologie di test svolti?
In questi vent’anni l’attività di puro testing non è cambiata molto, se non per il fatto che gradualmente negli anni abbiamo completato la gamma di prove globalmente richieste nel settore. Si parte dalle prove di “torque” in area meccanica ed ai controlli metallurgici e di integrità del processo di ricalcatura fino al controllo chimico ed ai PND superficiali, tipicamente liquidi penetranti. Ad oggi, il nostro laboratorio è dotato delle tecnologie e delle competenze per caratterizzare completamente qualsiasi elemento di collegamento meccanico.
Con quali figure all’interno delle aziende dialogate maggiormente?
Le nostre interfacce sono tipicamente persone coinvolte nel controllo qualità, si tratta di un settore non necessariamente innovativo ed anche ripetitivo lato testing, ma che richiede un’accurata pianificazione, considerando i volumi di test condotti. Non per niente, abbiamo investito massicciamente nella digitalizzazione dei processi di controllo della produzione e nel monitoraggio delle commesse.
Ad oggi con diversi clienti dialoghiamo con interfacce tecniche che con noi stanno sviluppando dei pacchetti tecnici trasversali da proporre ai diversi utilizzatori finali del settore. Operiamo quindi non solo come esecutori delle prove, ma anche come tecnici competenti nella definizione e strutturazione di piani prova dedicati. Il dialogo continuativo e aperto con il cliente è essenziale.
Sperimentiamo con i distributori di viteria aeronautica, su vasta scala, l’approccio che abbiamo avuto con altri clienti in termini di supporto tecnico nella definizione del piano di controllo, proposta già in essere con altri clienti su viteria commerciale, prodotti comunque presenti nel settore aeronautico e nel settore automotive.
Per quanto indichi, non tanto le prove ma proprio la richiesta di mercato in termini di servizio sta potenzialmente cambiando, come si struttura il pacchetto di servizio così inteso? quali sono i punti critici di queste attività?
Il tutto è nato poco più di tre anni fa, dopo gli incidenti aerei del recente passato è incrementata la necessità di controlli anche nella viteria commerciale che storicamente nel settore era considerata in “free-pass” con un controllo chimico eseguito dal fornitore del lotto. In questo frangente, abbiamo supportato il cliente nel capire la struttura e sequenza di controllo e le prove minime necessarie legate alle normative ISO di riferimento. Lato cliente, spesso mancano figure verticali con competenze per strutturare dei piani di test; per questo interveniamo a supporto. Ovviamente la statistica di controllo e la definizione del lotto di ispezione sono a carico del cliente come previsto dalla norma ISO 3269, ma come laboratorio possiamo mettere la nostra competenza a supporto della definizione di questi piani prova. Con alcuni clienti abbiamo portato avanti questo approccio arrivando alla totale nuova definizione del programma di testing con schede di controllo lotto totalmente riviste per commessa specifiche. La nostra volontà è quella di contrattualizzare con il cliente questa modalità di supporto/servizio, di modo da rendere il più snello possibile il flusso di produzione.
Oltre alla pura esecuzione del test, quali sono le fasi per la corretta definizione del numero, della tipologia e della sequenza di prove? In sostanza, quali sono le fasi necessarie prima del test vero e proprio e quali sono i punti critici di queste attività?
In primis serve avere conoscenza degli standard internazionali e nome proprietarie dei diversi clienti ed “end users”, a questo si accompagna la conoscenza delle criticità di processo e dei materiali coinvolti. Si parla di acciai altoresistenziali, acciai inossidabili che vengono definiti “corrosion resistance alloys”, genericamente definiti “CRES” nel settore. Per CRES si intendono anche superleghe a base nickel-ferro come la lega A286, non proprio un classico acciaio inossidabile! Ovviamente, immancabili sono le leghe di titanio ed alluminio, dopotutto l’alleggerimento è un “must” dell’industria aeronautica….e un aereo ha molte, moltissime viti!
Il pacchetto di prove deve essere preparato su classi di prodotti e materiali e deve essere proponibile come schema di controllo su delle schede standard. Questo permette di ridurre il tempo di verifica attività tramite uno schema di controllo solido che copre l’analisi chimica, le prove metallurgiche, meccanica ed in controlli non distruttivi, ad esempio con liquidi penetranti. Come dicevo, questo schema viene popolato con le quantità dal cliente.
A noi rimane poi la correlazione delle deviazioni e cambi di richiesta normativa. Si parla di un settore dove la normazione si è accumulata negli anni, con pochi aggiornamenti e “manutenzioni” del quadro normativo e conta parecchio l’esperienza nel valutare il componente ed i suoi requisiti di testing.
Il settore si muove ad altissima velocità e con urgenze puntuali legate alle linee di montaggio. In tutta questa preparazione delle attività, analisi tecnica dei lotti che arrivano, i test non sono ancora partiti e una volta pianificati tutti dettagli tecnici del controllo parte l’attività del laboratorio. Di fatto è necessario definire un flusso di controllo che abbia un suo binario specifico.
Dal punto di vista di un laboratorio, quali sono le tipologie di richieste di test che aumenteranno nei prossimi anni? Oltre ai test che tradizionalmente vengono svolti, vedete un aumento di richieste di qualche tipologia di prova particolare?
Il settore automotive vive molto di controllo “meccanico” della viteria, ma vedo in crescita la necessità di controllo metallurgico di superficie e la compatibilità dei materiali con l’idrogeno nei processi di fabbricazione e rivestimento; questo nell’settore auto, ma anche nel settore aerospazio. Allo stesso modo il controllo PND superficiale sarà in crescita soprattutto in area aeronautica. Per non parlare del tema della funzionalizzazione delle superfici, che credo aumenterà molto di interesse nei prossimi anni.
Dal punto di vista del cliente, quali sono i vantaggi a breve e a lungo termine che riconosci in termini di qualità del prodotto e di costo complessivo del suo componente?
Principalmente, assicurare la garanzia di qualità del prodotto e semplificare le necessità di controllo, dato che il settore dei fasteners ha catene di fornitura molto lunghe. Il nostro servizio punta a questo.
Muoversi nel settore del testing in questi contesti è complesso per una spesso non compresa, seppur chiara, distribuzione di responsabilità tra chi produce, distribuisce e controlla. Oltre questo una garanzia di tempi certi nella verifica dei lotti in collaudo. Quando si parte da una base contrattuale solida, in TEC Eurolab possiamo coprire le attività di base con un lead time di 7gg. E sulle urgenze possiamo essere molto più rapidi.
Molti centri di service possono erogare attività di testing, ma il vero valore aggiunto che possiamo dare è accompagnare il cliente nel definire puntualmente un piano prove “sartoriale” sulla base delle effettive necessità di prova e adattarsi rapidamente a variazioni. Insomma, operare continuamente per cercare il giusto bilanciamento tra flessibilità dei tempi di attraversamento, qualità del servizio di testing erogato e rispetto delle scadenze concordate.