thermal barrier coatings
Case studyTEC EUROLAB
Caso di studio sui rivestimenti a barriera termica
Il reparto prove meccaniche di TEC Eurolab presenta un nuovo caso di studio su Termospruzzatura e Thermal Barrier Coatings.
Termospruzzatura – Introduzione generale
La termospruzzatura indica una famiglia di processi di deposizione di rivestimenti spessi, metallici o non metallici. Tutte le tecniche si servono di una torcia per riscaldare la materia prima, prodotta con la composizione chimica desiderata, fino allo stato fuso o semi fuso, e per proiettarla verso il substrato da rivestire.
La morfologia dei rivestimenti termospruzzati è prevalentemente lamellare e deriva dall’impilamento degli splat strato dopo strato, in direzione ortogonale alla superficie del componente. Prima di un qualsiasi processo di termospruzzatura, si richiede sempre una certa rugosità sulla superficie allo scopo di garantire un migliore aggancio meccanico al rivestimento. Le particelle termospruzzate infatti, una volta giunte sul substrato a temperatura più bassa, si deformano e possono contrarsi attorno alle creste di rugosità in fase di raffreddamento.
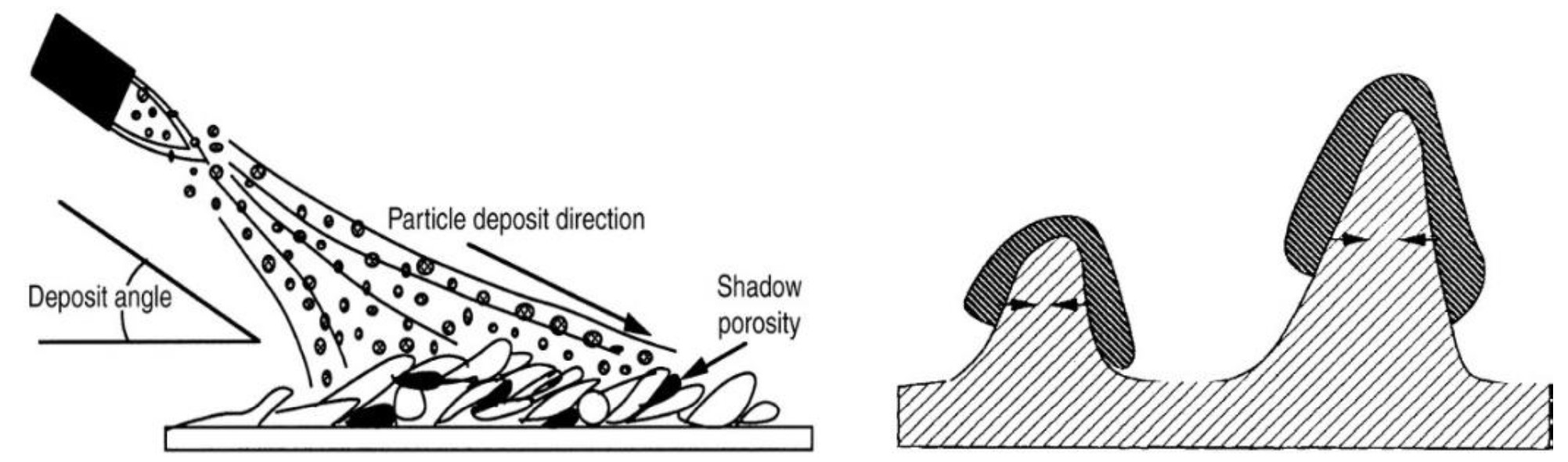
I rivestimenti termospruzzati contengono tipicamente: pori, particelle parzialmente fuse o infuse, splat (particelle completamente fuse e deformate), fasi metastabili e (nel caso di rivestimenti metallici) inclusioni di ossidi.
La porosità del riporto è influenzata dai parametri di processo e dalle dimensioni della materia prima: partendo da polveri con distribuzione granulometrica fine e sufficientemente stretta (es. 5-22 μm), la fusione delle stesse risulta ottimale e si ottiene un rivestimento denso, adatto ad applicazioni antiusura e anticorrosione. Viceversa, le particelle grossolane e con distribuzione più ampia (es. 45-125 μm), a parità di energia fornita al getto gassoso, fondono solo parzialmente e danno luogo ad un riporto poroso, con peggiori proprietà meccaniche ma idoneo all’isolamento termico.
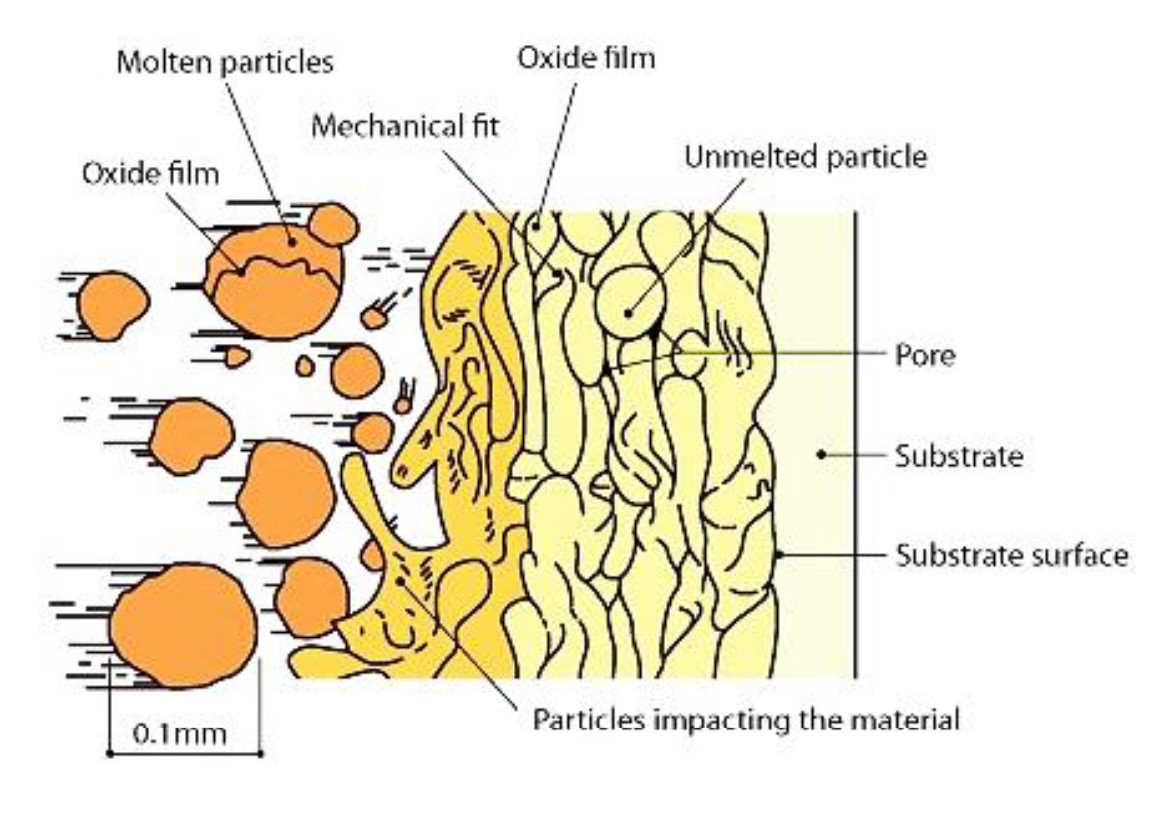
Case Study: Thermal Barrier Coatings (Barriere Termiche)
Descrizione
Le TBC sono rivestimenti multi-strato, funzionali e protettivi, applicati su substrati metallici allo scopo di abbassare la temperatura superficiale e rallentare l’ossidazione. Lo strato superiore è detto top coat e funziona da isolante termico, mentre il bond coat intermedio, oltre a migliorare l’adesione del top coat, garantisce una buona resistenza a ossidazione e corrosione ad alta temperatura.
Utilizzi: liner dei bruciatori, condotti di transizione e palette nei primi stadi di turbina (sezione calda) di gruppi turbogas e motori aeronautici.
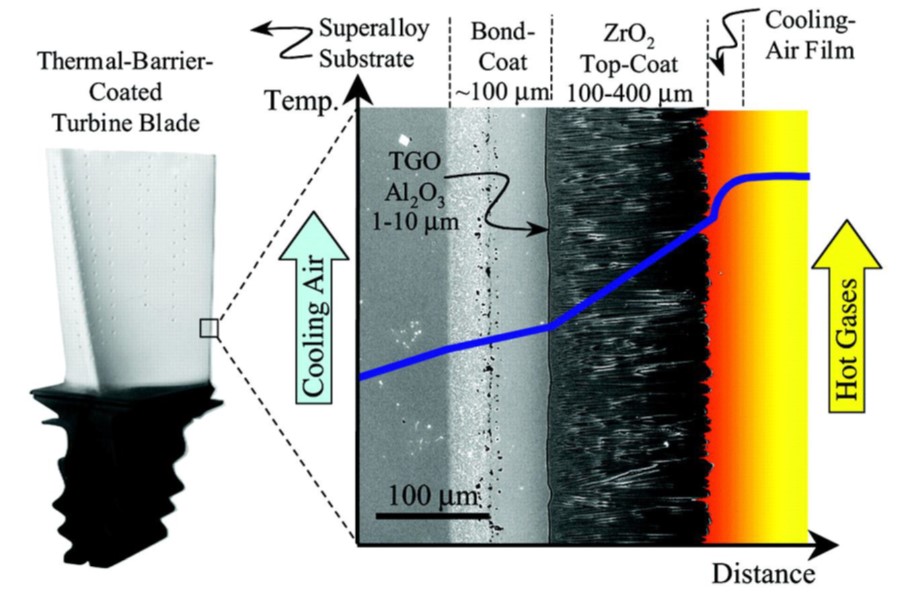
Tecniche di caratterizzazione
1. Prova di conducibilità termica
Il gradiente termico lineare imposto dalla TBC si spiega attraverso l’equazione di Fourier sulla conduzione del calore:
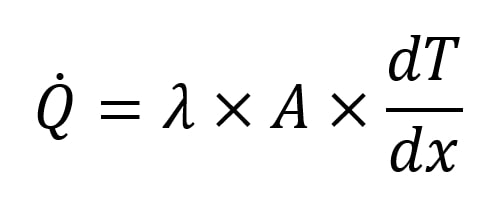
Si nota che la riduzione di temperatura è tanto più efficace quanto minore è la conducibilità termica del materiale e quanto maggiore è lo spessore della TBC. Il substrato, generalmente costituito da superleghe a base Nickel (Inconel, Hastelloy, ecc…), e il bond coat sono costituiti da materiali metallici e danno contributo quasi nullo all’isolamento termico. La TBC permette l’isolamento del substrato grazie all’elevata porosità al suo interno e alla sua bassa conducibilità termica, in quanto ceramica.
Normativa di riferimento ASTM E1461
La conducibilità si ottiene indirettamente dalla formula:
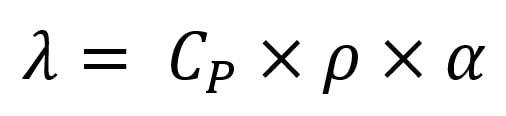
dove Cp è il calore specifico, ρ è la densità e α è la diffusività termica. Quest’ultima è misurata solitamente mediante flash laser riscaldando il campione solo da un lato, inducendo un gradiente di temperatura.
2. Test di trazione o Test di adesione
Il pull o bond test è una prova di trazione che permette di misurare il grado di coesione interna al rivestimento e/o l’adesione di quest’ultimo al substrato. Il valore di bond strength definisce l’integrità e la durabilità dei componenti rivestiti tramite Thermal Spraying, i quali dipendono sia dalla coesione interna tra gli elementi del rivestimento (strati e lamelle) sia dall’adesione all’interfaccia tra riporto e substrato.
Normativa di riferimento ASTM C633-13
Una volta depositato il rivestimento da testare su di un campione cilindrico (“bottone”), si procede all’incollaggio di entrambe le facce (superiore e inferiore) a due supporti cilindrici (tappi di accoppiamento) in acciaio inossidabile di diametro 1″, i quali successivamente vengono sottoposti ad un test di trazione.
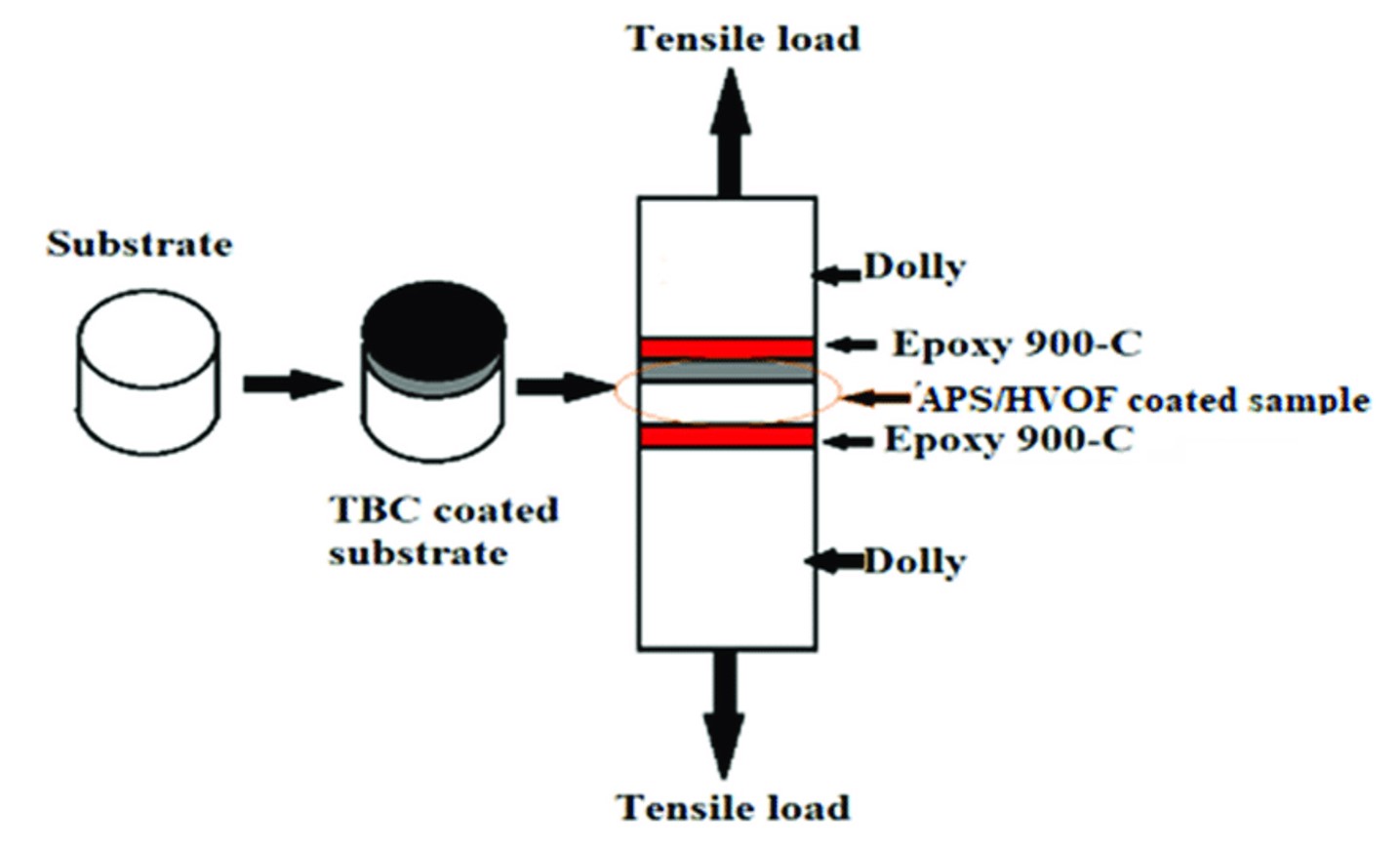
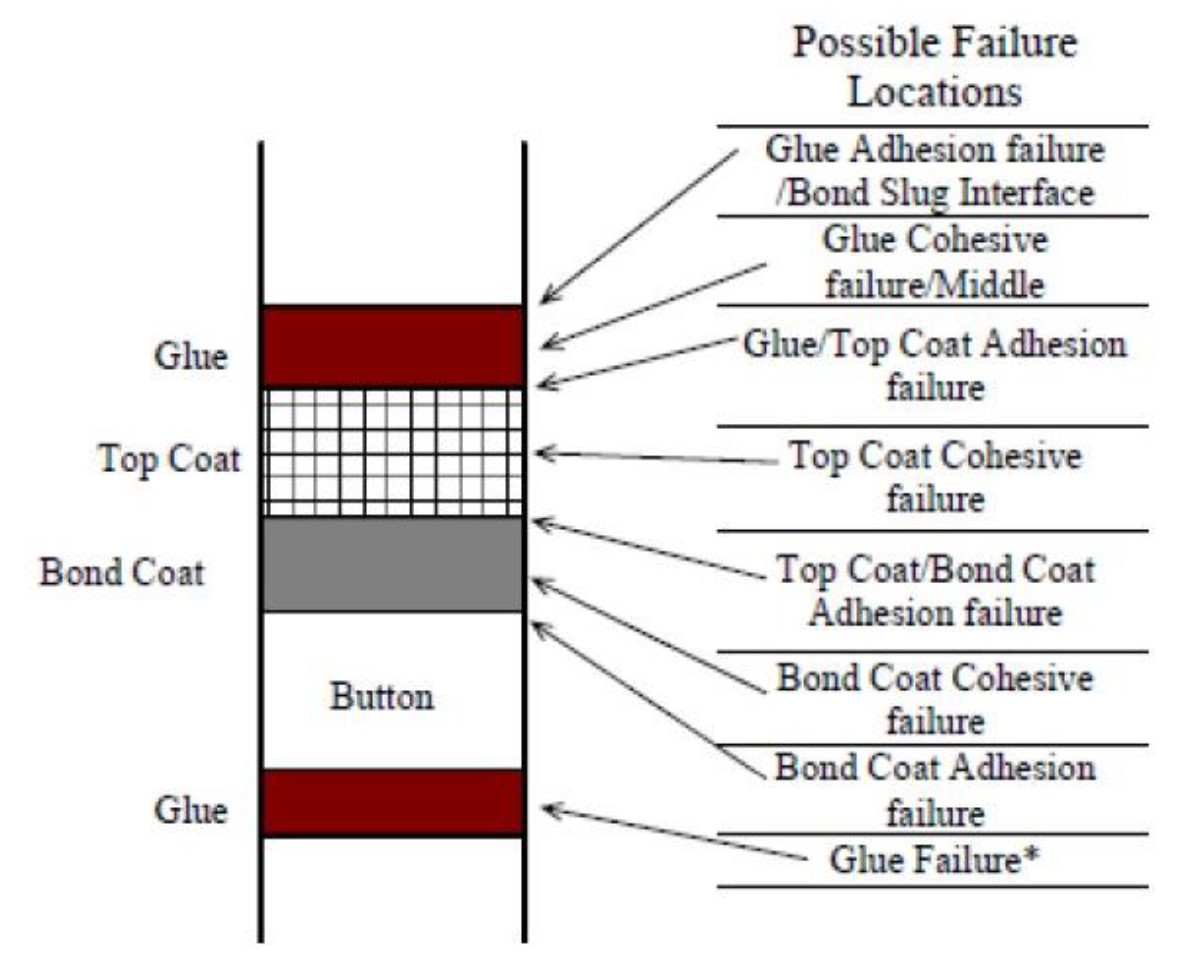
La rottura avviene nella parte più debole del campione: se essa è localizzata all’interfaccia tra il substrato e il rivestimento si ottiene un’indicazione dell’adesione a trazione di quest’ultimo, se invece si trova all’interno del rivestimento allora il valore di bond strength rappresenta il grado di coesione interna allo stesso.
3. Prova di ciclaggio termico
Le dilatazioni e le contrazioni termiche inducono stress all’interfaccia tra materiali diversi e rappresentano una delle cause principali di fallimento delle TBC. All’interfaccia con la TGO (Thermally Grown Oxide), generata dall’ossidazione del bond coat all’interfaccia con il top coat, si verifica infatti la nucleazione di cricche in direzione parallela al substrato, provocando la cosiddetta coating spallation. Ad alta temperatura inoltre il top coat subisce fenomeni di sinterizzazione e ciò riduce la sua capacità isolante.
Normativa di riferimento ISO 14188
La prova si applica per misurare la resistenza ai cicli di riscaldamento e raffreddamento.
Solitamente per questo tipo di prova si definiscono criteri di accettabilità basati sull’analisi visiva del danneggiamento subìto dal rivestimento (es. rigonfiamenti, cricche, distacco parziale o totale del rivestimento).
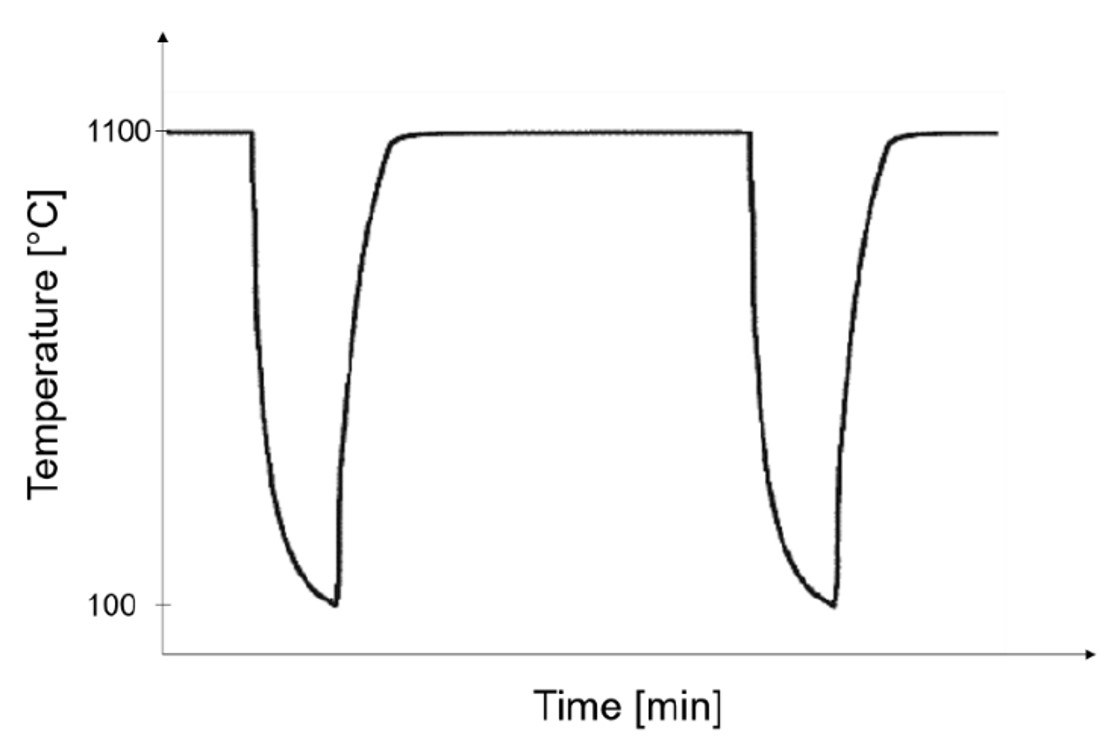